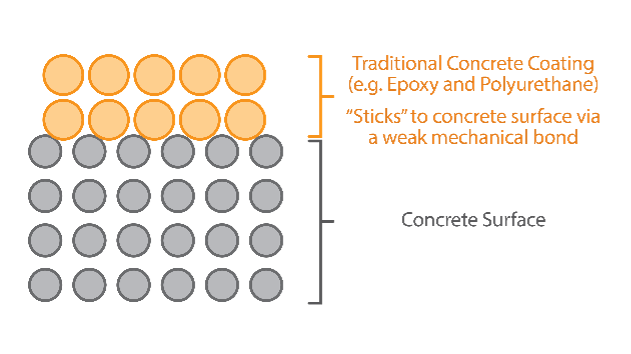
Bonding
What is the difference between adhesion strength and bond strength and why does it matter? The difference is that bonding means a permanent chemical attachment (e.g., ionic or covalent bonding) between two surfaces. Adhesion is a temporary state between two surfaces that does not involve any chemical bonding.
In short, it matters because if you want to build or repair something, you want it to be durable and last. The longer it lasts, the lower its “true” cost, which means its lifecycle cost to operations. The problem in the current market is that the term adhesion is badly misunderstood and misused, to the point that it has created its own mythology, the “adhesion bond” concept.
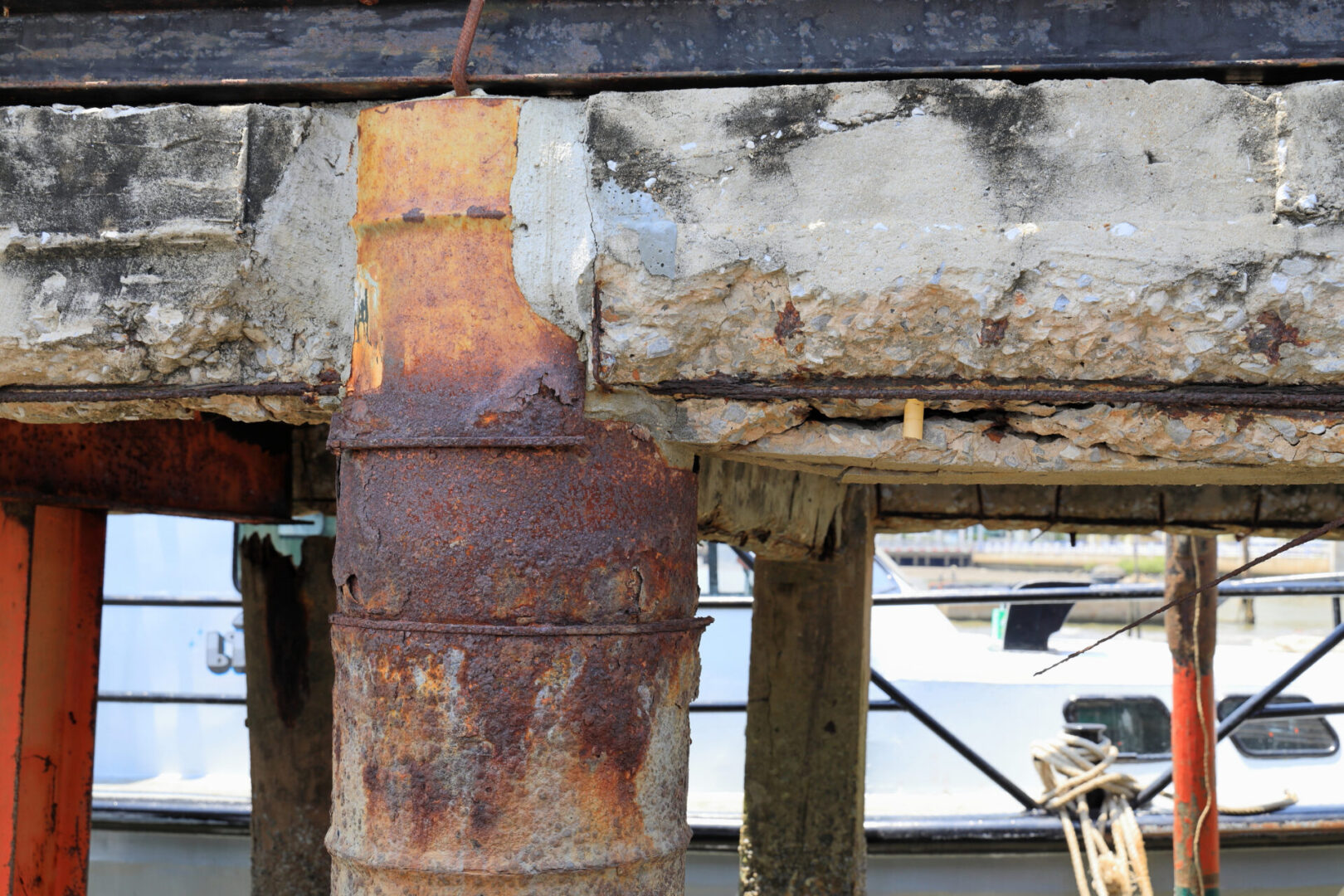
Ironically, it is not uncommon to hear the term “adhesion bond,” when in fact the phenomenon of adhesion does not include any actual chemical bonding. Adhesion is really just a coating’s ability to be “sticky.” This stickiness is sometimes due to a chemical trait that uses Van der Waals forces, a type of physics that basically means that two surfaces “like each other” and will stick together for a brief time while optimum conditions last. This is a temporary condition that rarely last long in industrial settings.
When a coating “adheres” at the surface interface of the concrete, there is an “adhesion zone” which is vulnerable to being damaged by the presence of humidity from under the slab, or cleaners and water from the cleaning process. In the presence of other chemicals, including simple water/humidity, the two surfaces may stop “liking each other” and the adhesion between the two surfaces dissolves away. Harsh cleaning chemicals generally accelerate this dissolving process. This is one reason epoxy and other plastic coatings delaminate from concrete surfaces. In reality, plastics cannot chemically bond to concrete, as their chemistries are too dissimilar. This is also a reason many coatings require the installation of a vapor barrier because the moisture is a known cause of failure.
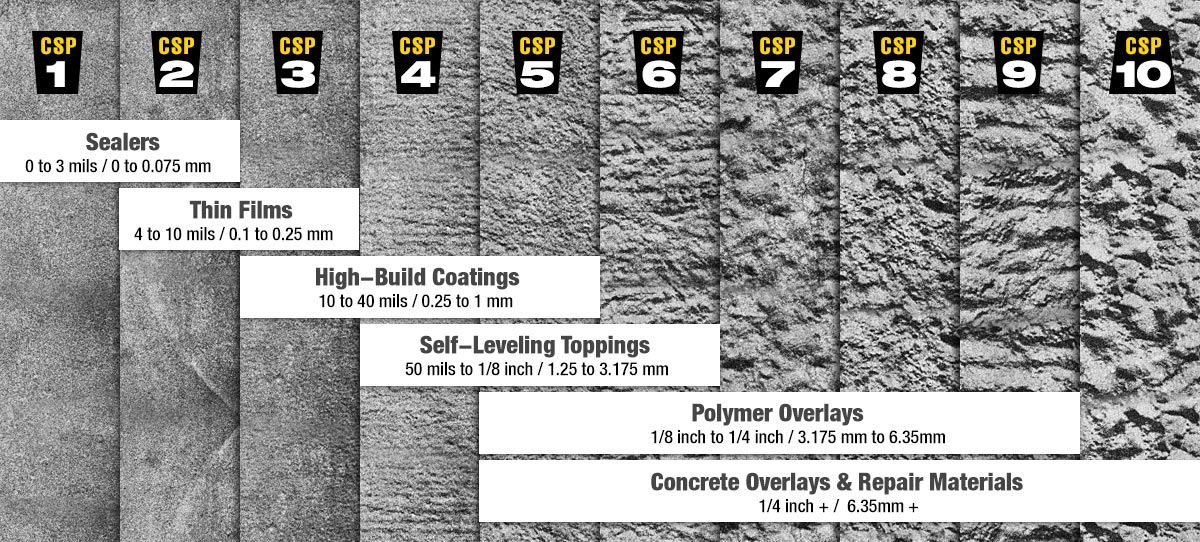
Epoxies and other plastic coatings can have a “mechanical bond” which is not a chemical bond, but just the ability to grab something and hold on. This requires the substrate concrete to be scratched, abraded, or shot blasted in order to create a surface that has enough rough surface area for the epoxy to wrap around and hold onto. Unfortunately, the damage caused by this installation technique makes concrete dramatically more porous, thus more capable of holding dirt and contaminants, and more prone to biological infection long-term.
Ceramic Surface Treatments (CSTs) Fully Compatible with Concrete
Zirconia's Ceramic Surface Treatments (CSTs) are inorganic and share chemical and behavioral traits with concrete, for instance both are silicate based, and therefore share expansion/contraction coefficients. The CSTs penetrate, cross-link, and form an ultra-stable ceramic polymer composite with concrete elements at the surface. CSTs are atomically attached to concrete elements (sand, aggregate, and cement paste) so they are not able to detach. This process transforms the weak, chemically unstable hydrated calcium silicate into a stable alumina-zirconia-silicate composite (similar to granite).
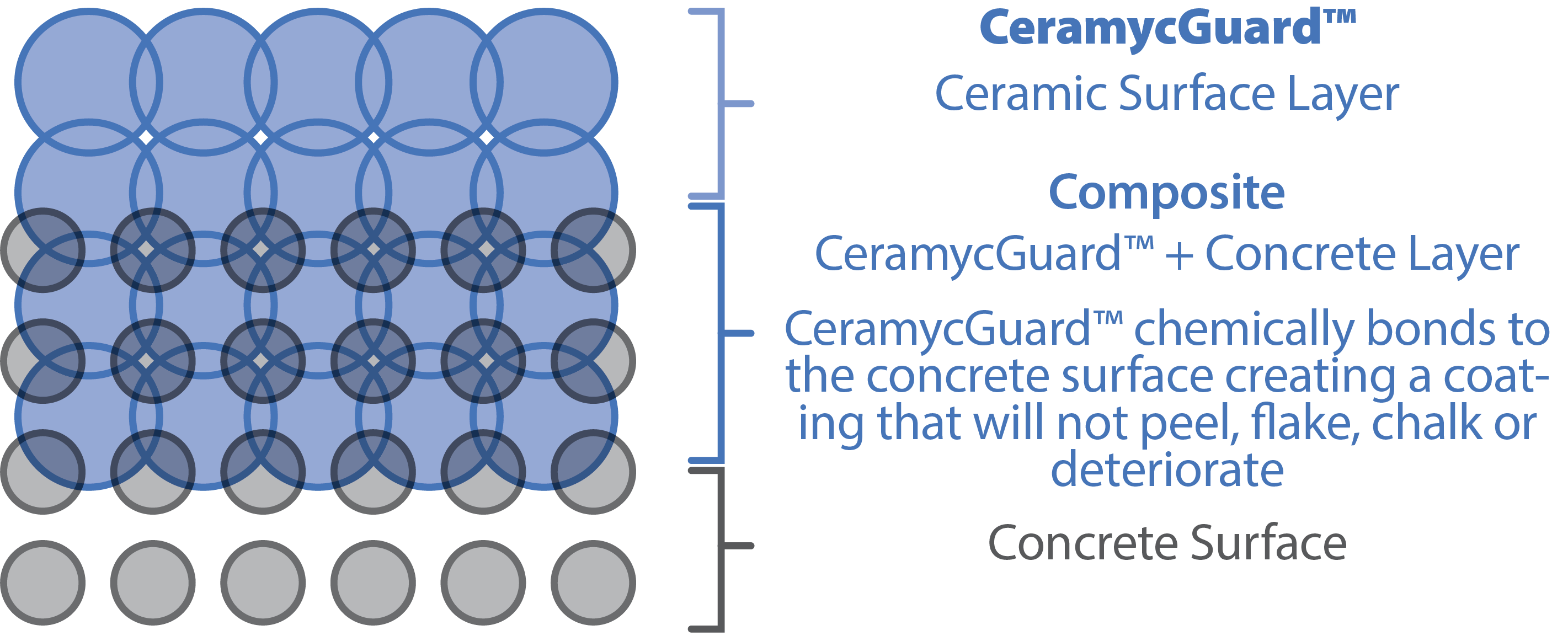

This means that Zirconia’s CST systems are not affected by water once they are cured. Moisture in the concrete does not harm it and it can be submerged in water without damage. Further preparation is reduce since the slab does not need to be dried out and there is no need to do advance preparation to provide profile for it to grab on to. For floors it means you just need to provide a light grind or sand to remove contaminants and leave a faint scratch pattern to provide more chemical reaction surface and not to provide “tooth” or profile for the coating to grab on to. Zirconia’s nano structure penetrates into the smallest openings like pores and cracks and bonds to all the elements exposed surfaces.